Stump Records
Record player built into a Redwood stump with audio digitization
For my capstone design course I wanted to make something that I would keep. I had seen too many mech-e projects that get built out all semester only to be parted out when all was said and done. So after mulling over a few ideas, I decided to make a record player. Sounds pretty mundane, right? Well, I would build this record plater into a stump that I cut myself from the Santa Cruz mountains, and this record player would also digitize and save your records to mp3 files on your computer. Now it sounds a little more exciting. I owe my peers Sepehr and Albert a huge thanks for their contributions to the project, as well as a thanks to Jacob and Dennis from the Etcheverry machine shop, and Twiggy from Jacobs Hall.
While not a revolution in terms of innovation, the project did allow me to deploy a wide range of skills I had accrued over my time at Berkeley. It would involve CAD/CAM, CNC work on both metal and wood, manual mill and lathe operations, waterjetting, firmware and software development, motor control, audio signal processing, UI/UX considerations, and more. A video of the project is shown below, as well as many more project details and photos.
I started by finding a nice downed Redwood tree on my buddy Aaron’s property. He was kind enough to help out with the search, and loaned me his chainsaw for the day. I brought the stump down to the lab and used marine epoxy to fill most of the gaps. This involved creating a duct tape barrier around it and letting the epoxy seep through the stump for several days.
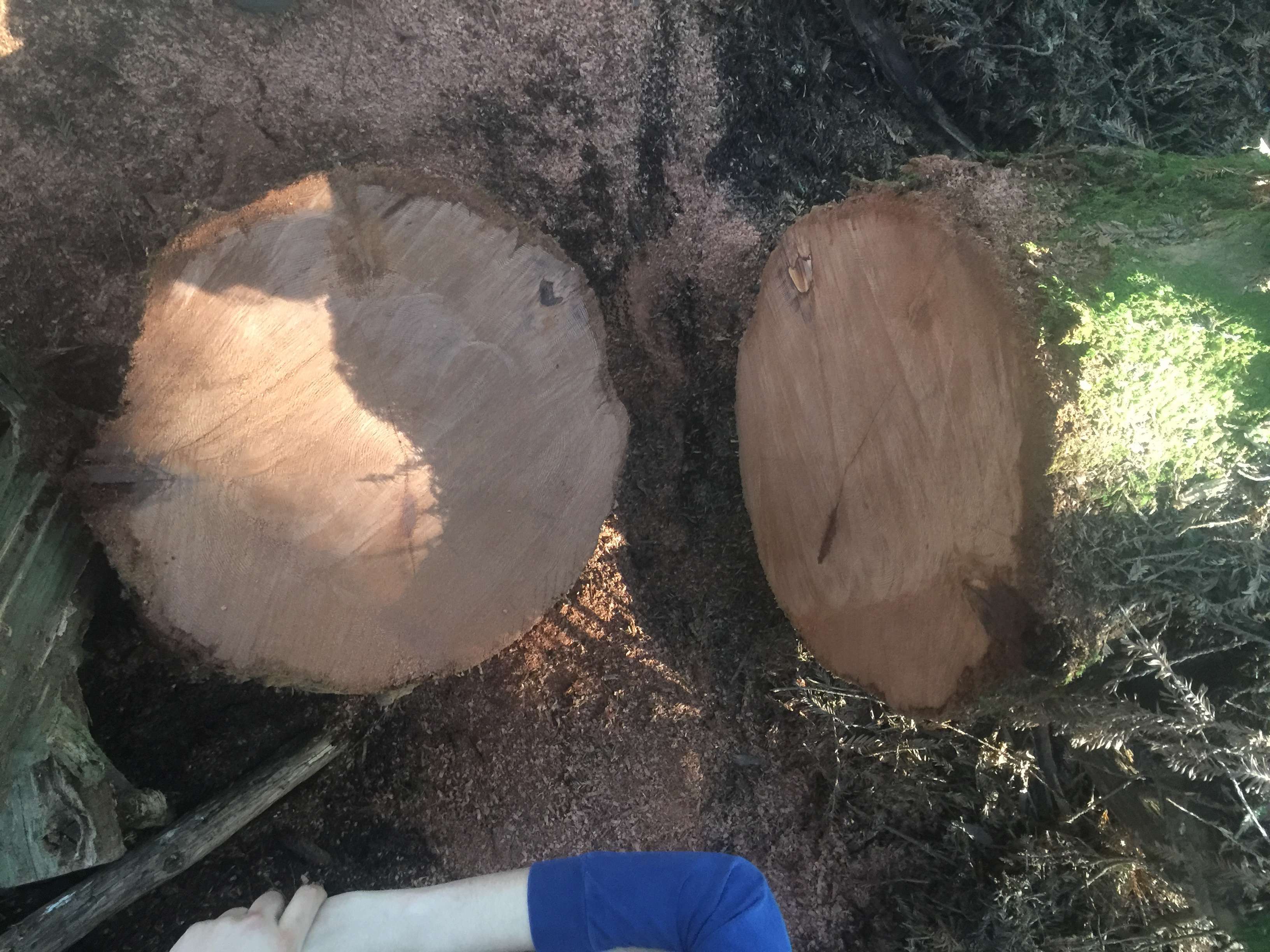

In the meantime, I tested hole sizes for bearings, worked on CAD, and developed toolpaths for the Shopbot CNC I would be using to cut the stump. It was a real challenge to figure out how to datum a super organic workpiece, there were no flat surfaces, no 90 degree edges, and the piece didn’t even fit in the Shopbot without some encouragement. Eventually, after weeks of work and dozens of hours on the Shopbot, I had the stump cut out to spec. It involved a lot of complicated jigging, some dowel placement in order to be able to flip the piece over and over, and templates taped on top of the work surface.
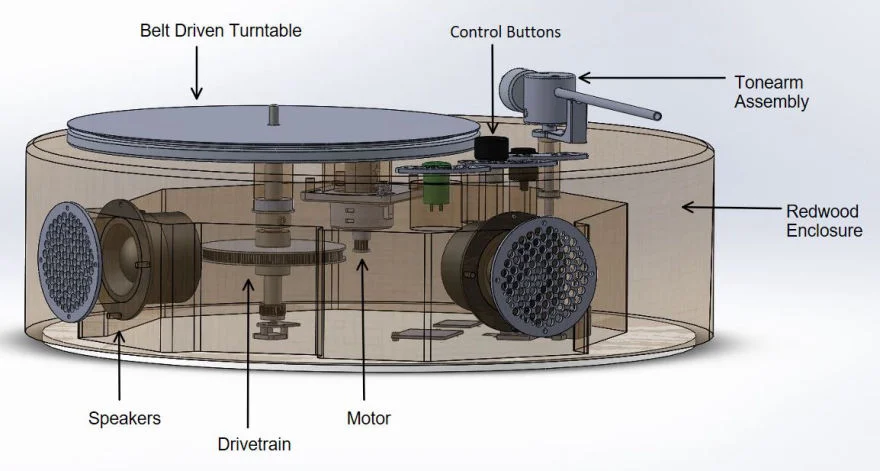
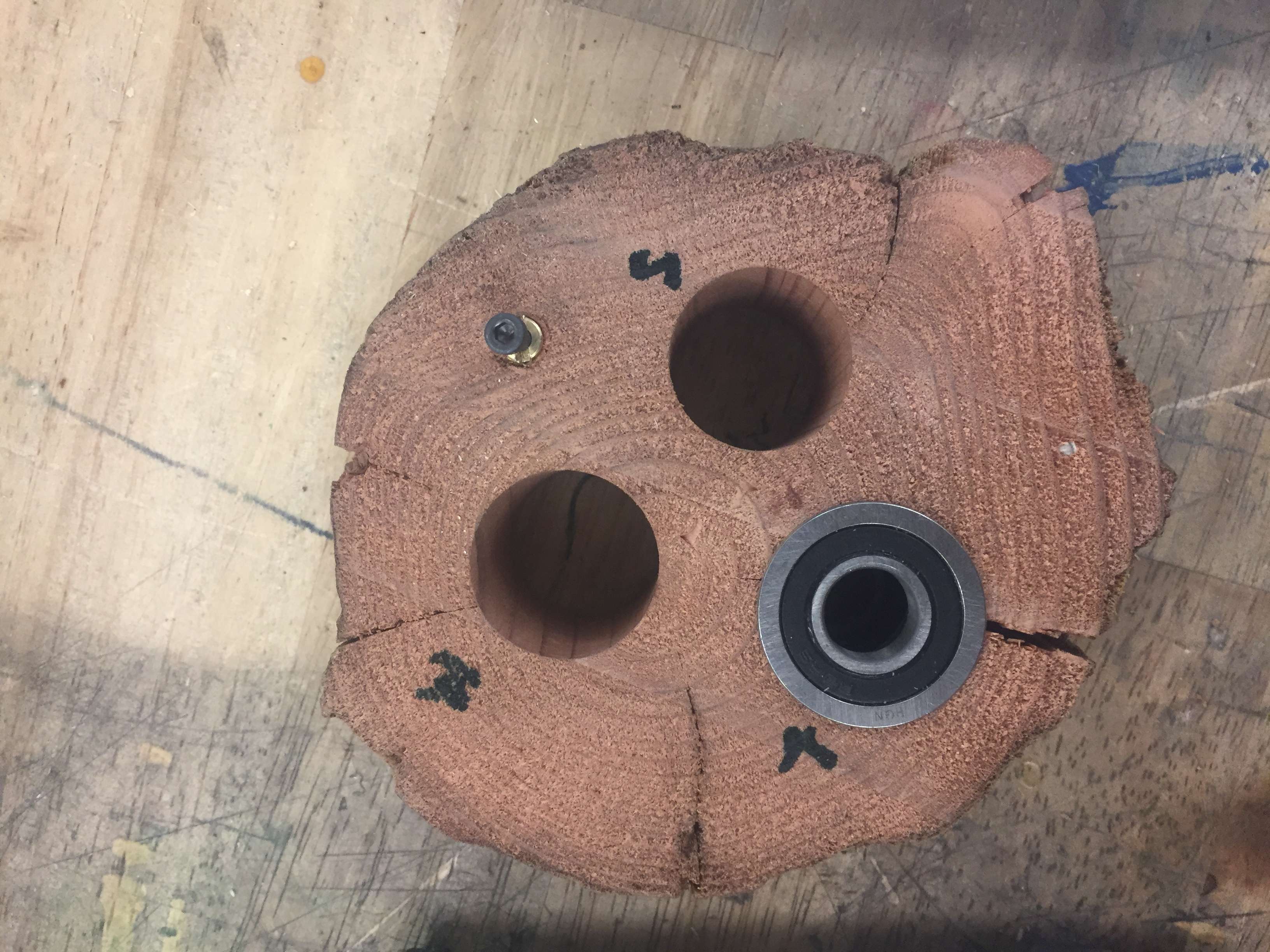
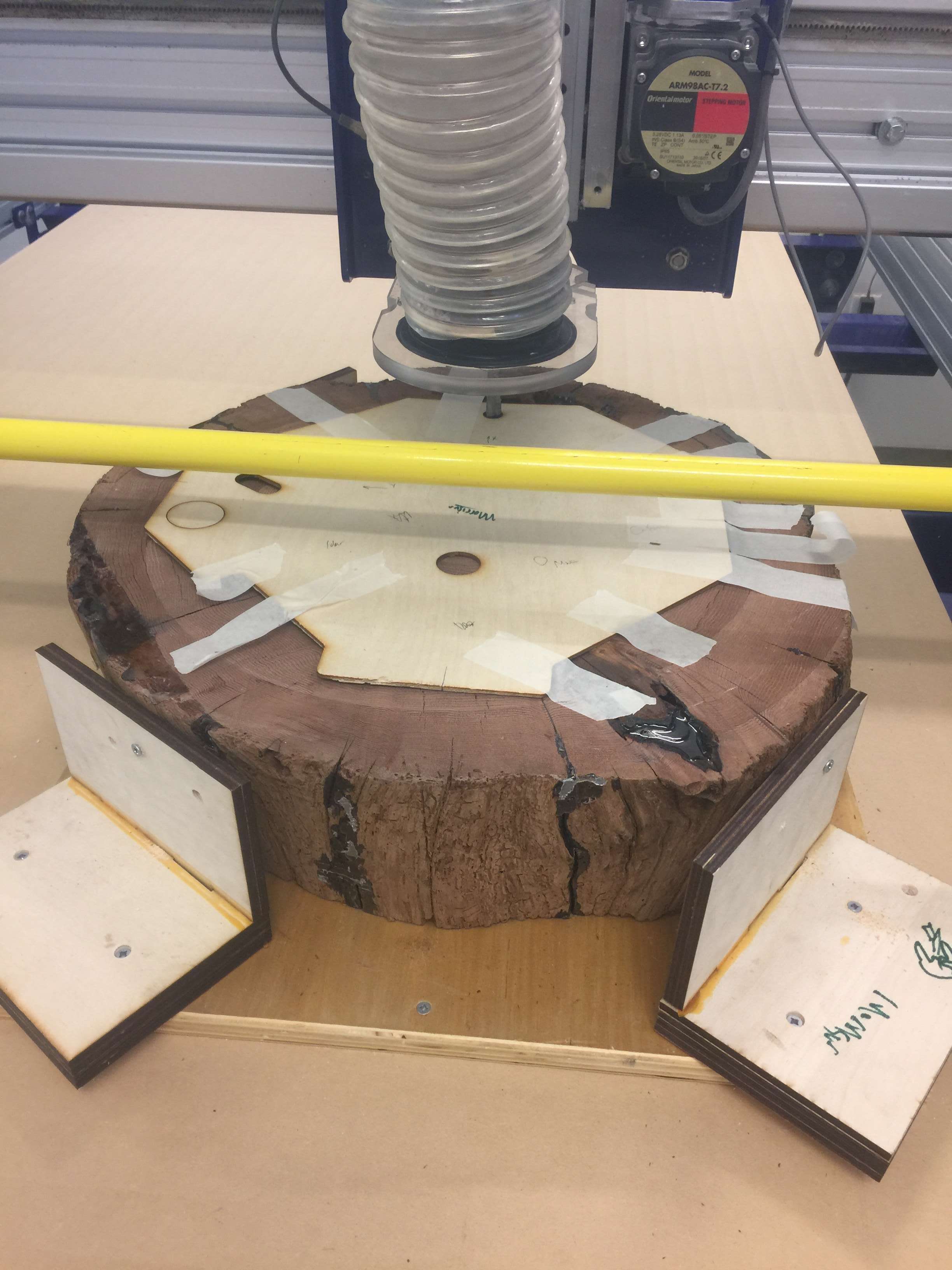
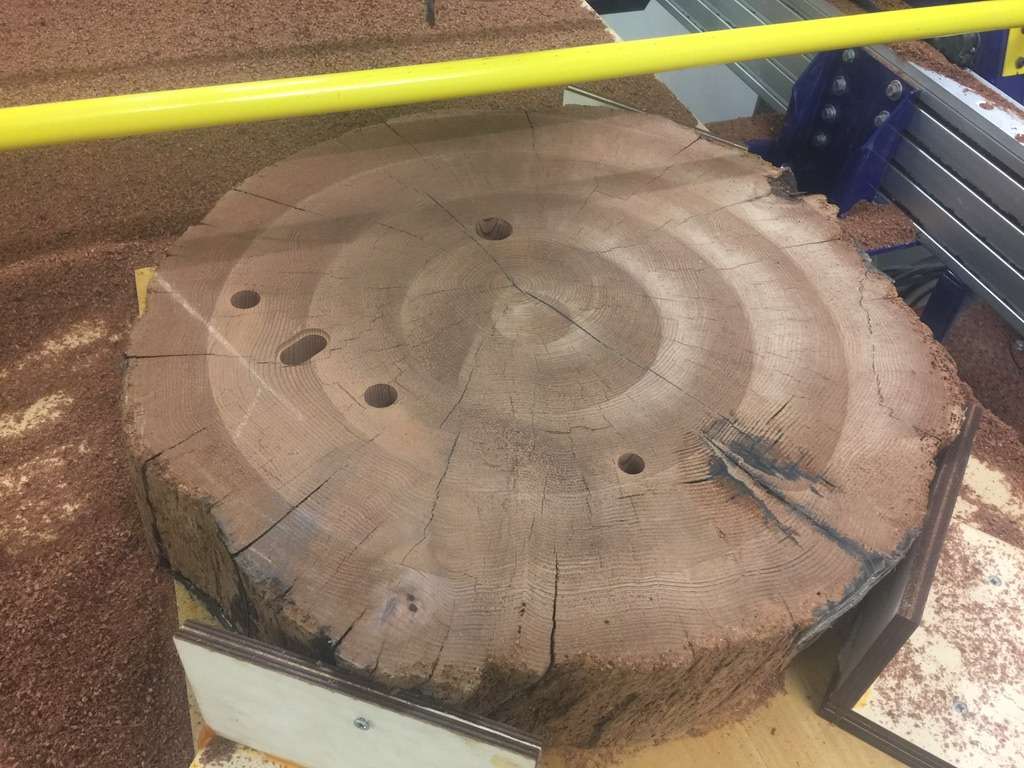
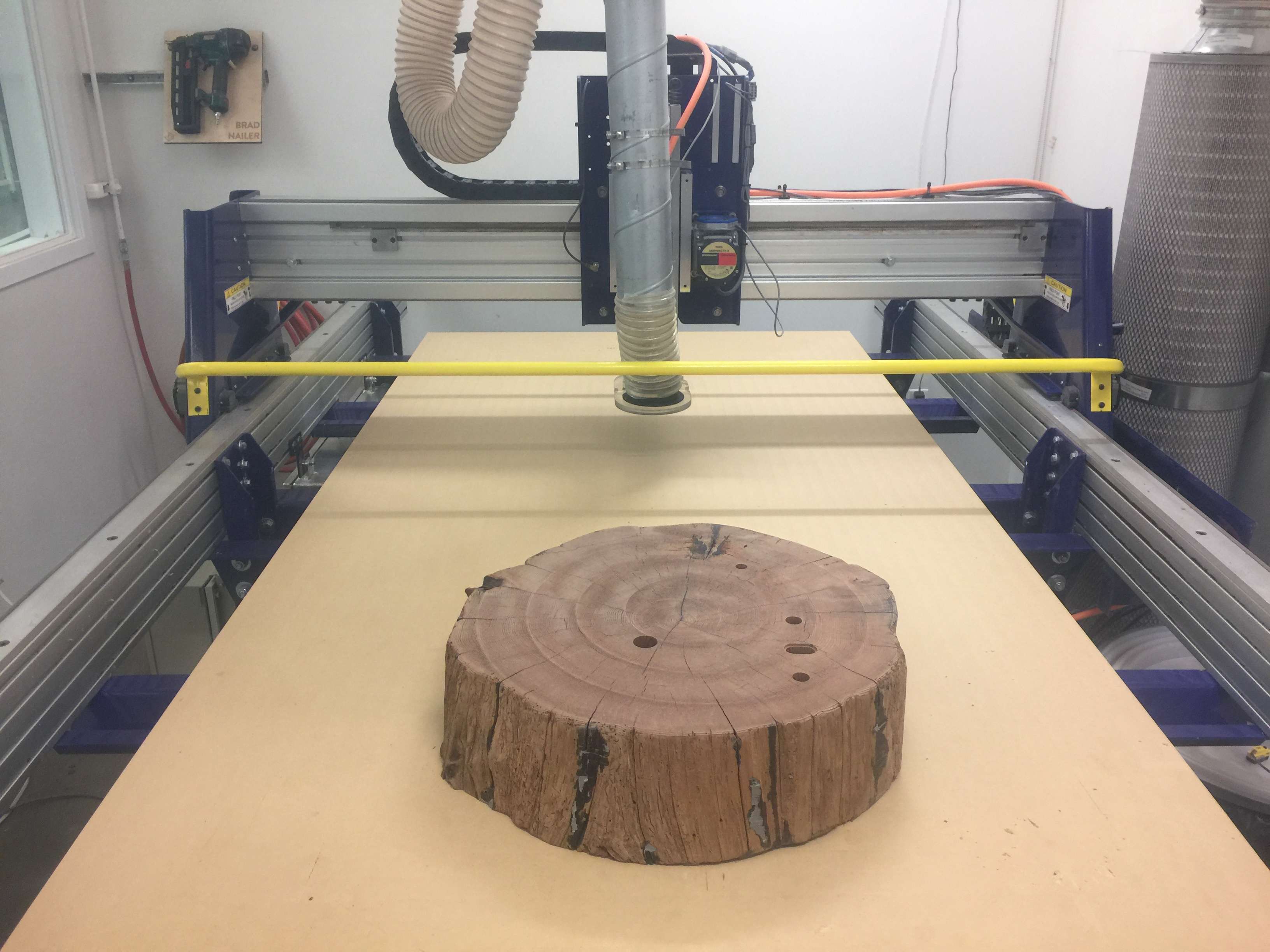
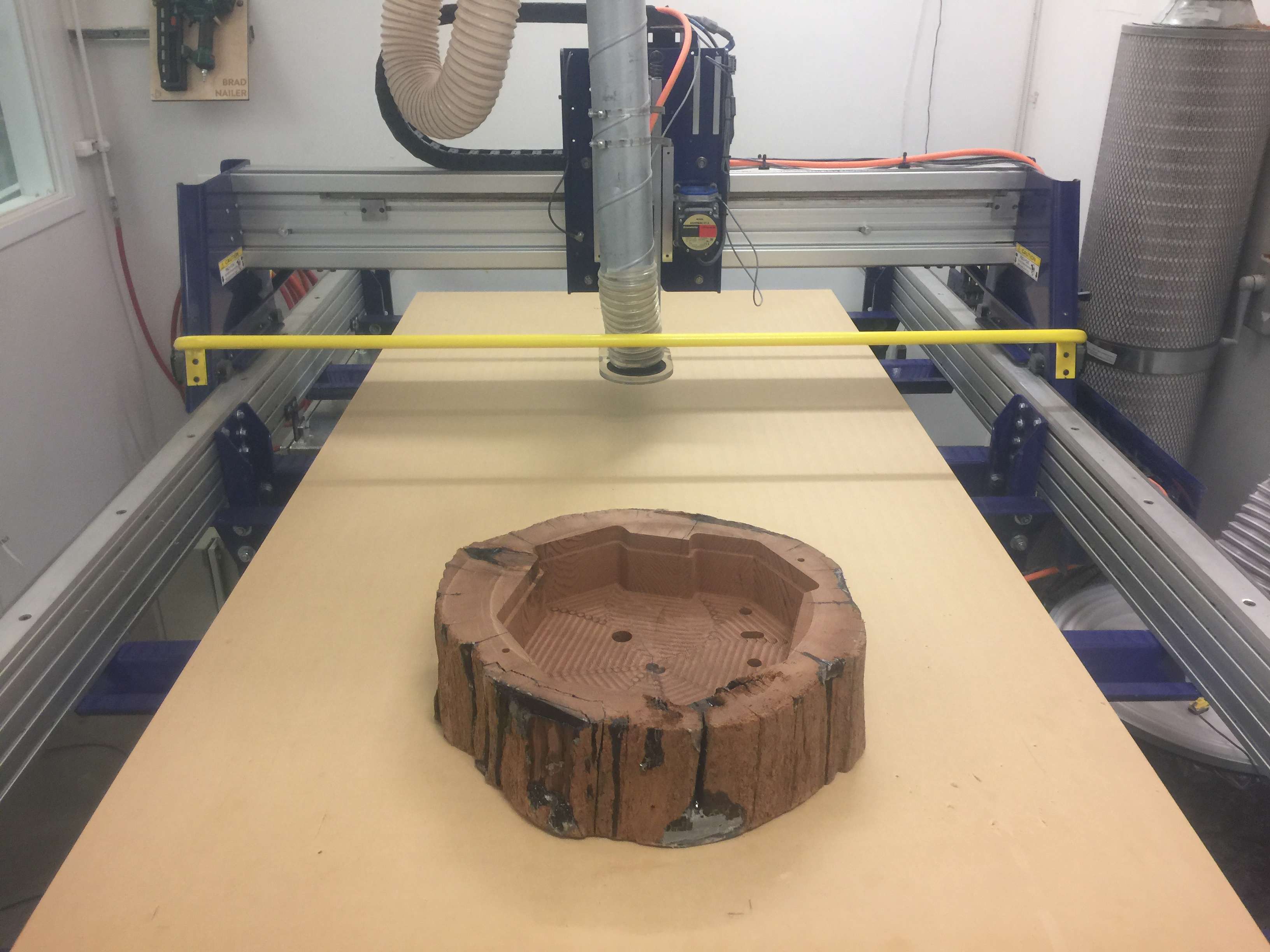
During all this time, I worked on fabricating the subassemblies, like the tone arm (which included an auto-stop feature to stop the record at the end of the album), all the metal components for the top of the piece, and the electronics housings. Albert helped a ton with figuring out all of the motor control stuff, and we also were able to figure out digitization. We were able to save the audio data real time to a microSD card on our microcontroller, and then read that data over serial to the computer and convert it to MP3 files.
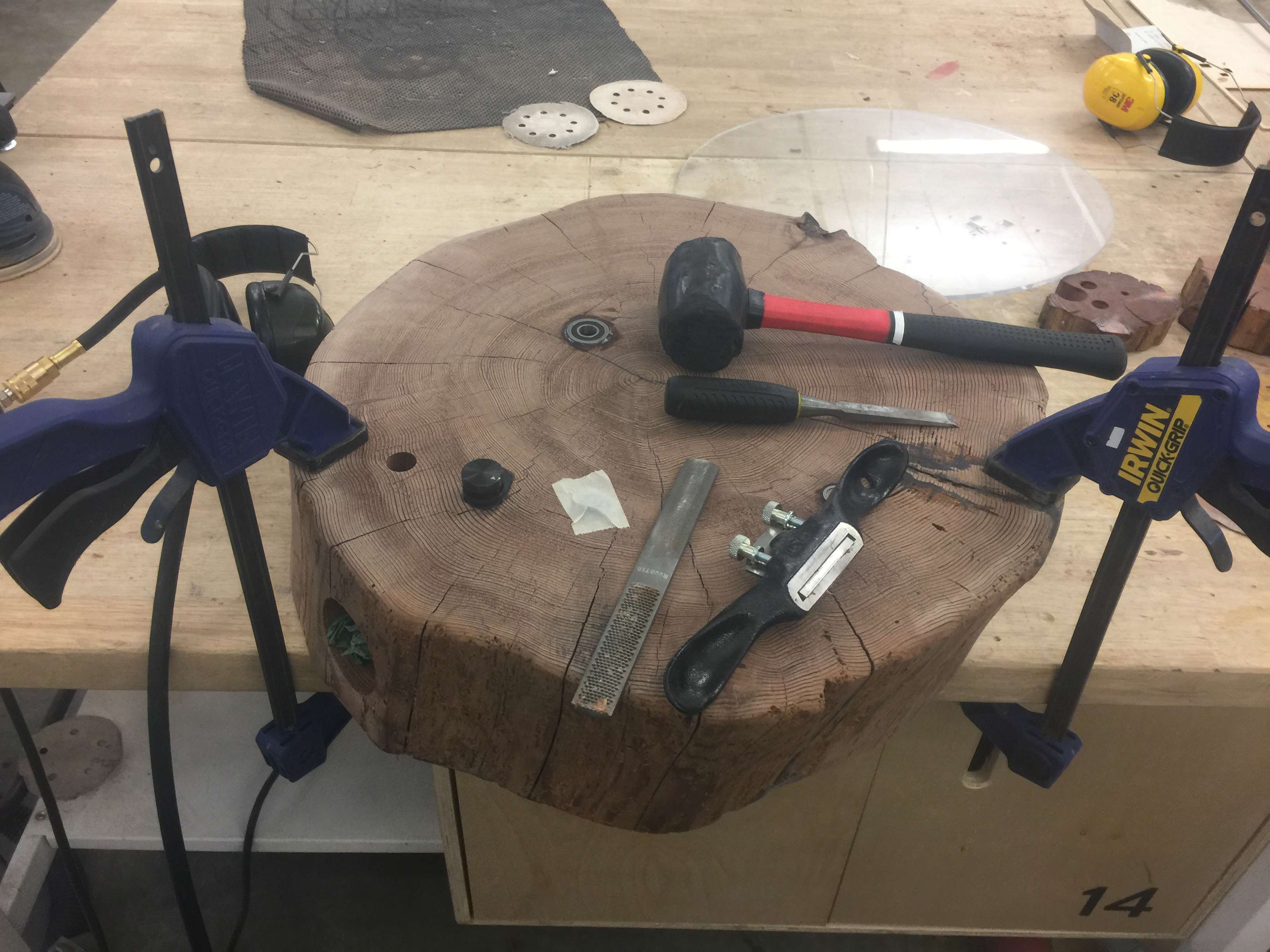
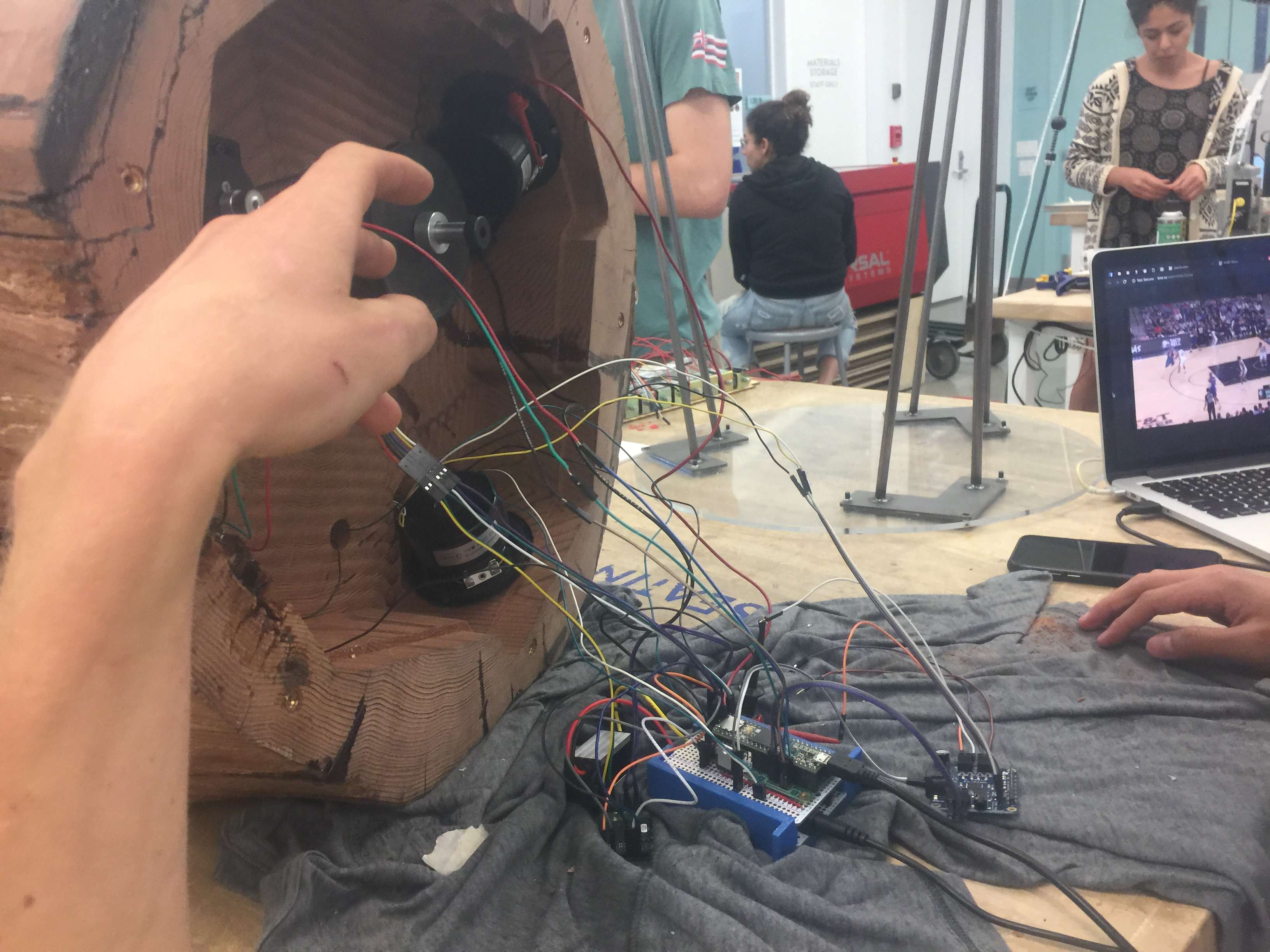
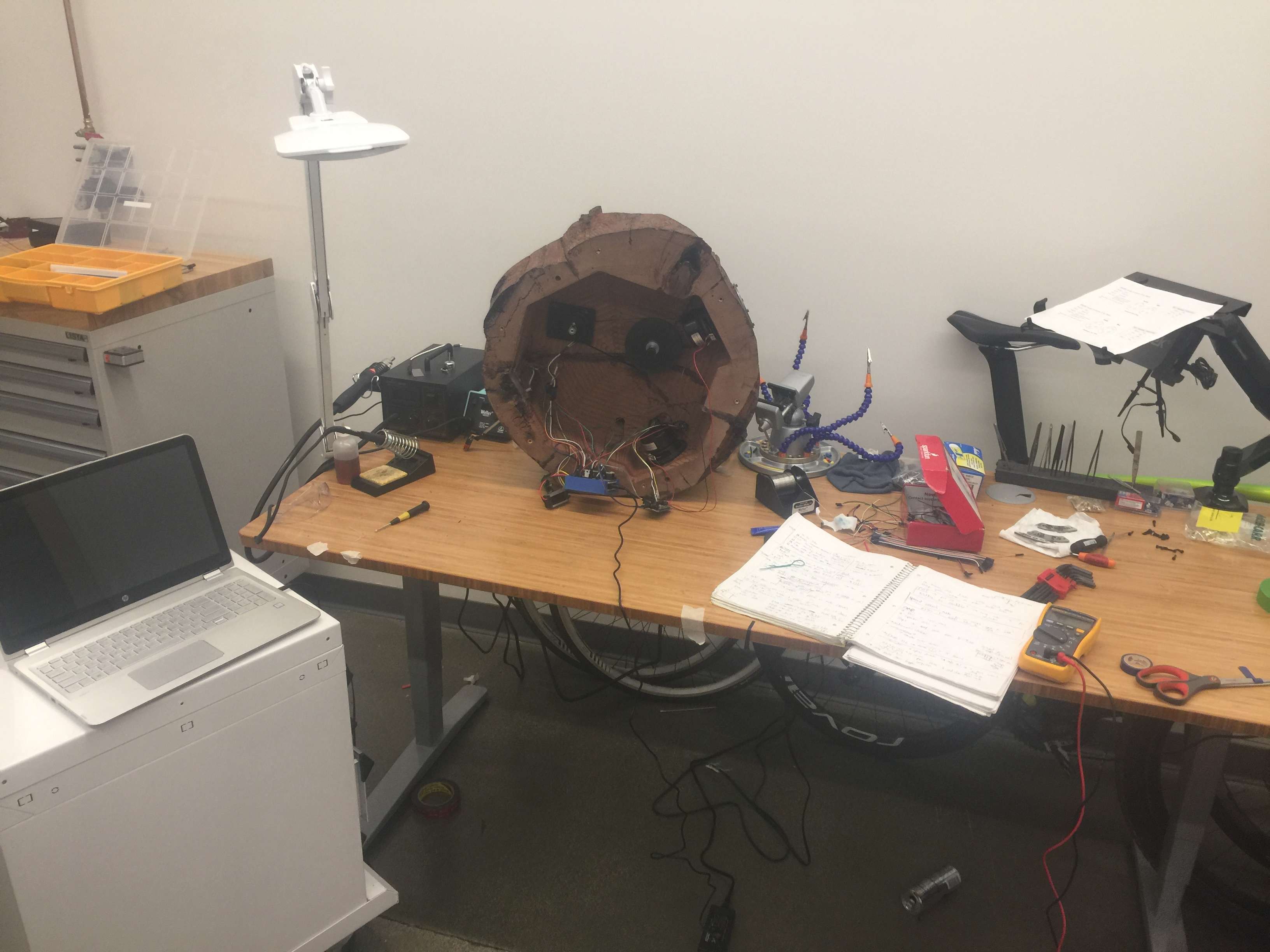
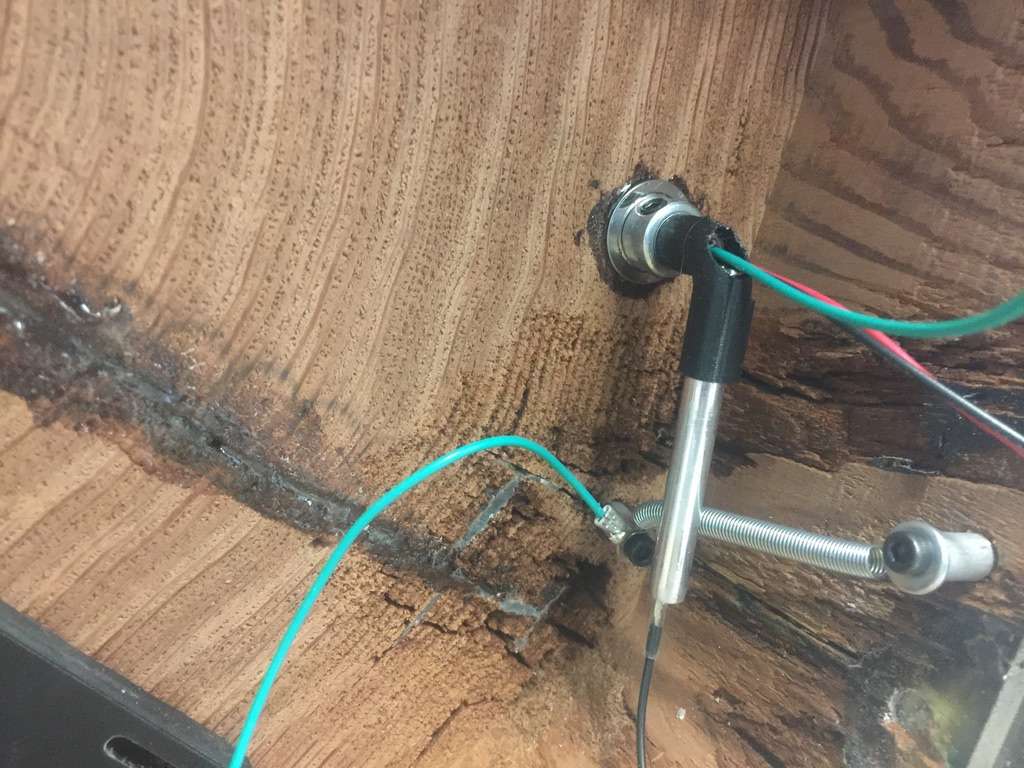
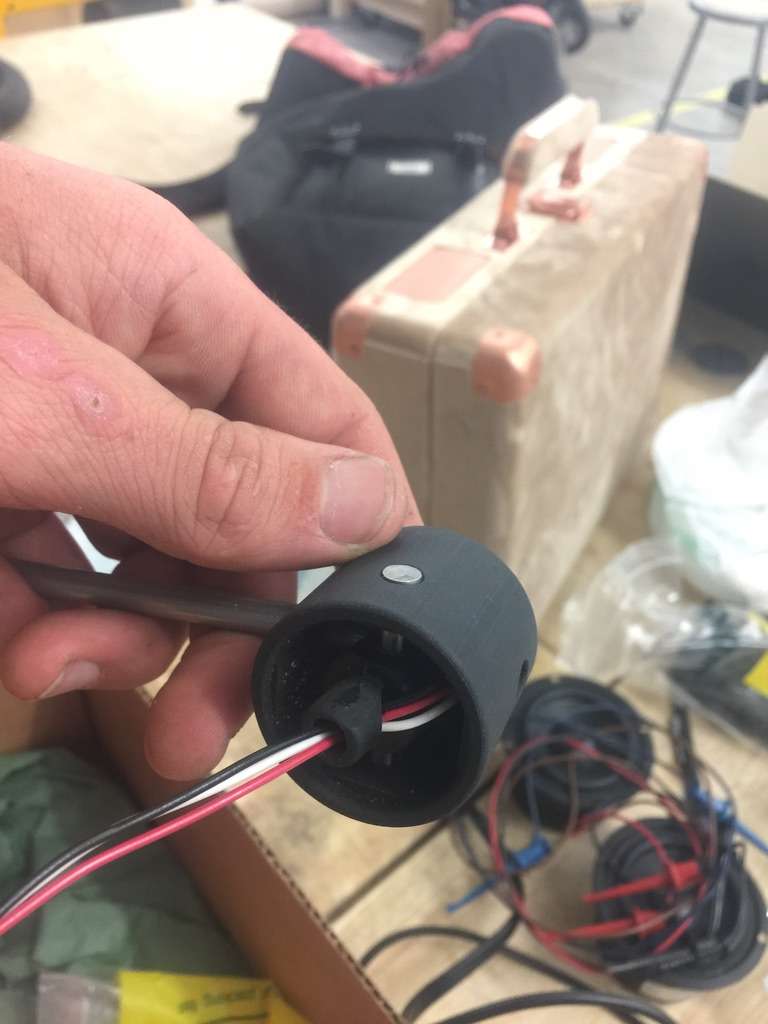
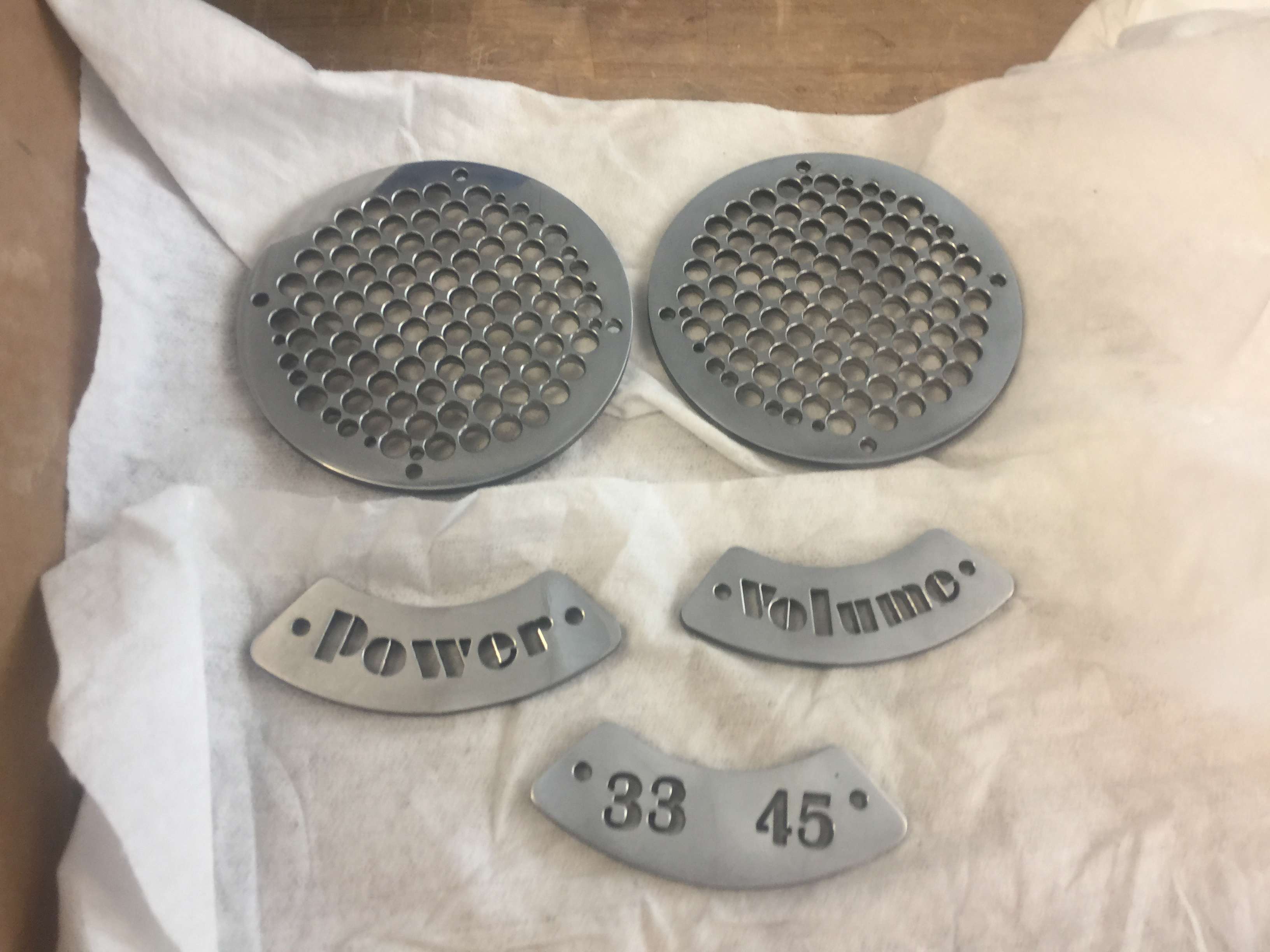
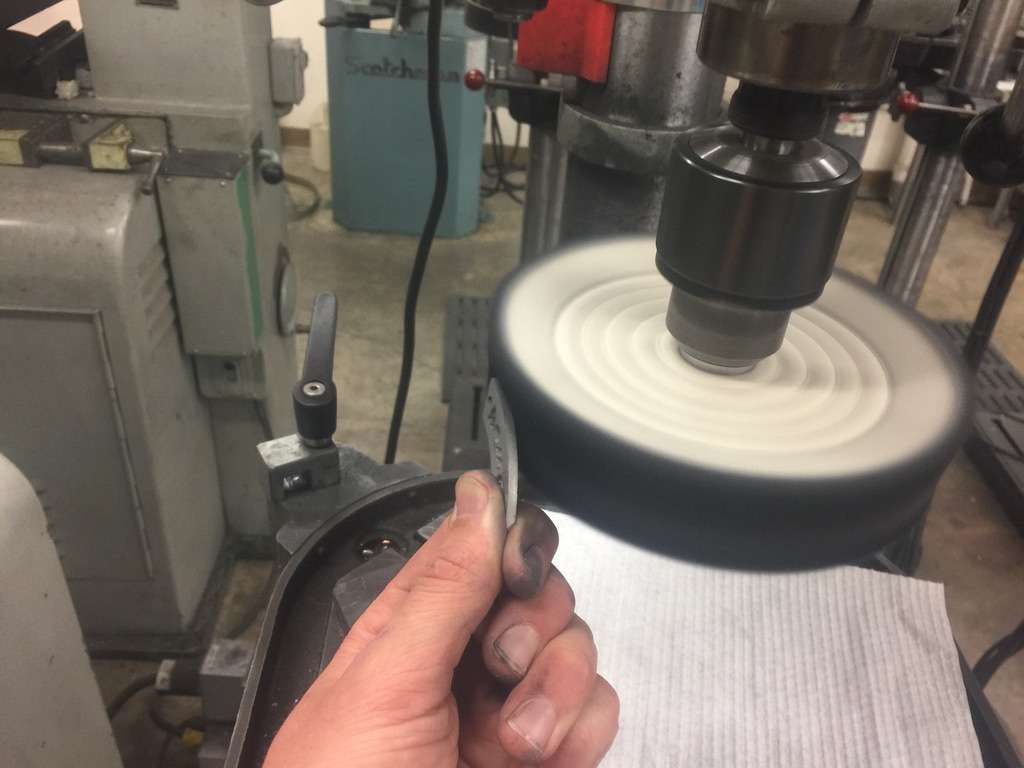
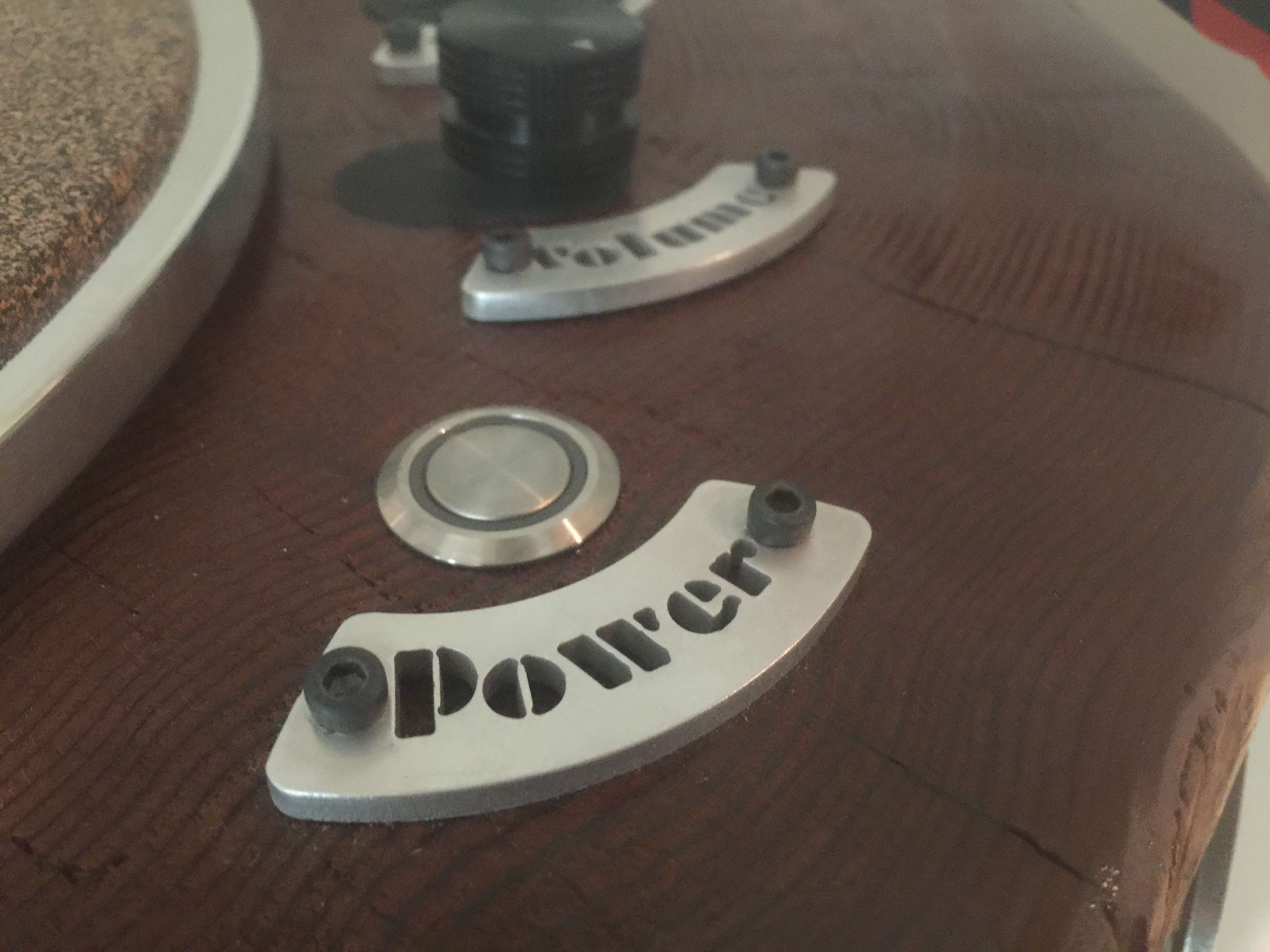
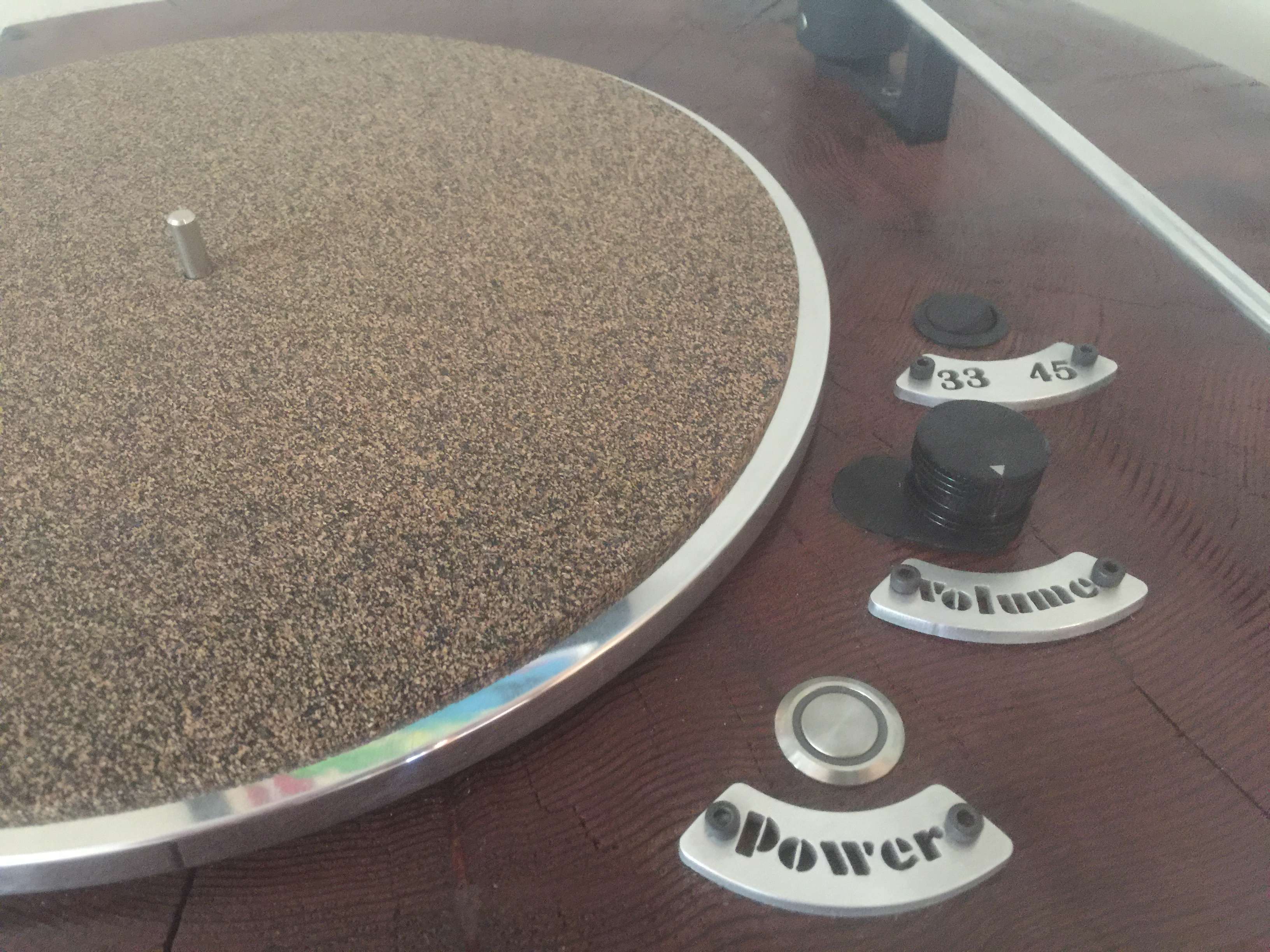
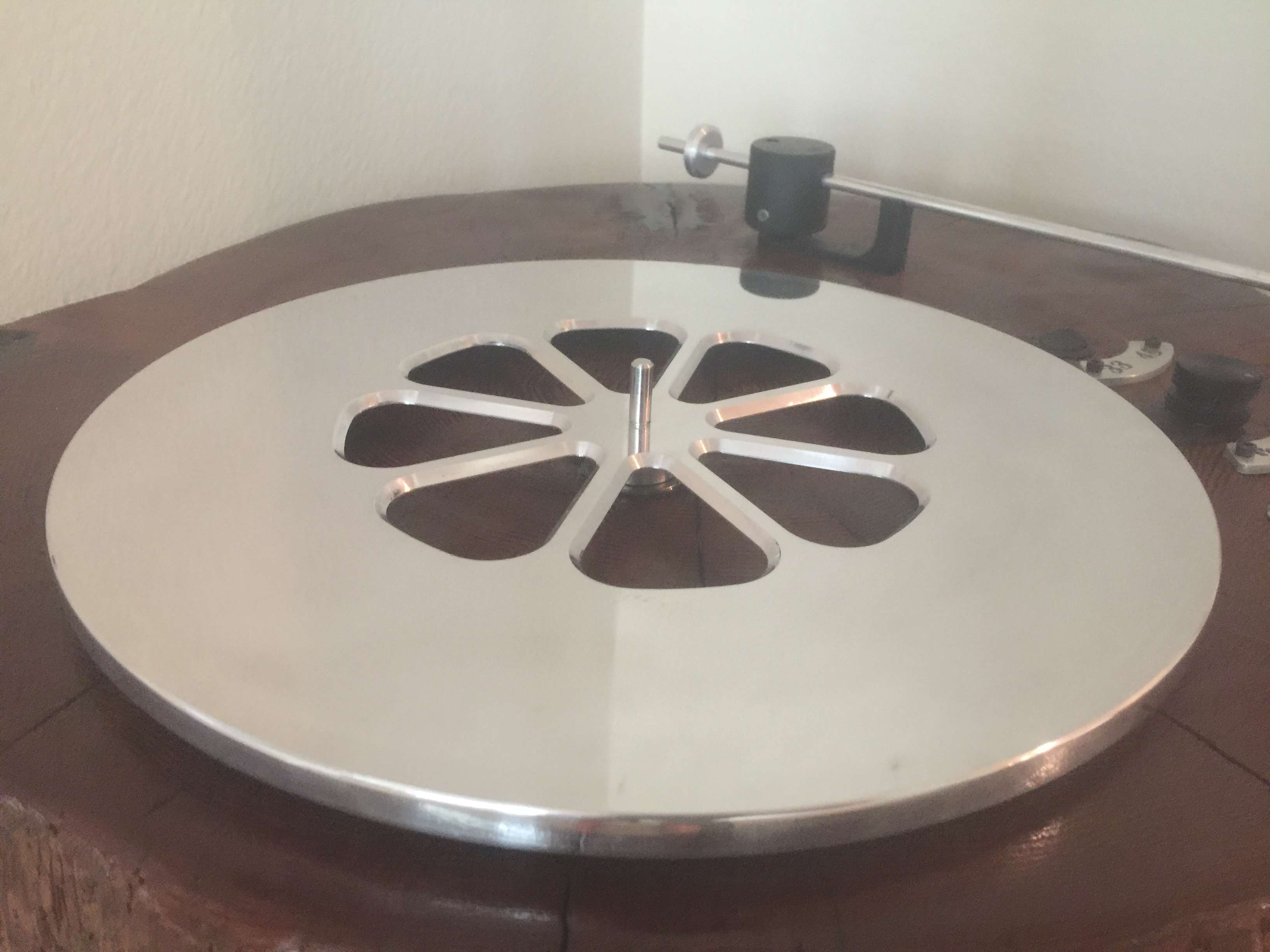
Eventually, it came time to assemble everything. I installed bearings, treated the wood with some stain and paste wax, installed all the subassemblies, and worked out various kinks. I housed all the electronics under the stump on a clear sheet of acrylic so that interested users could peer “under the hood.” It took about four months to go from concept to finished product, and I never want to make another record player again.
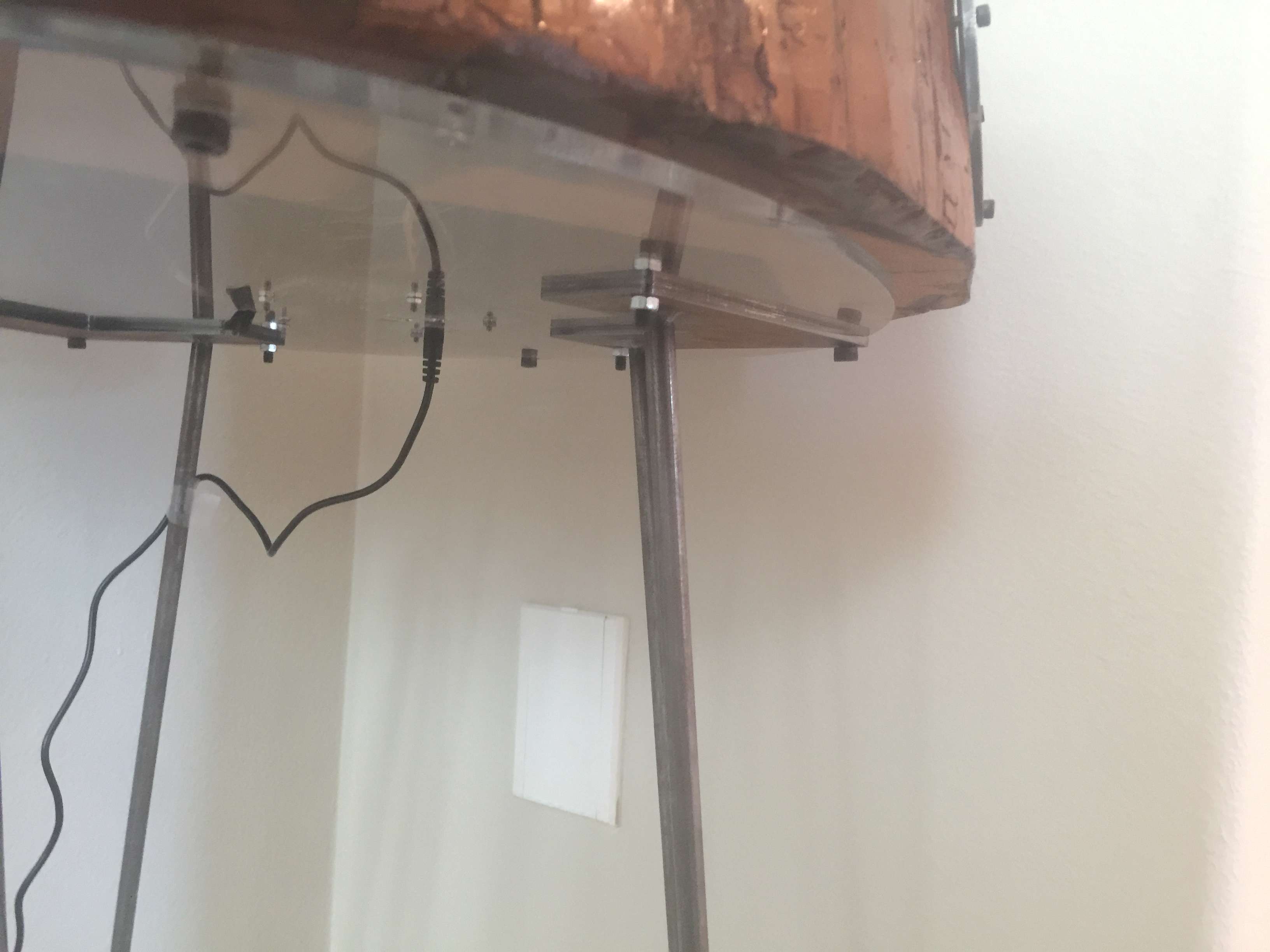
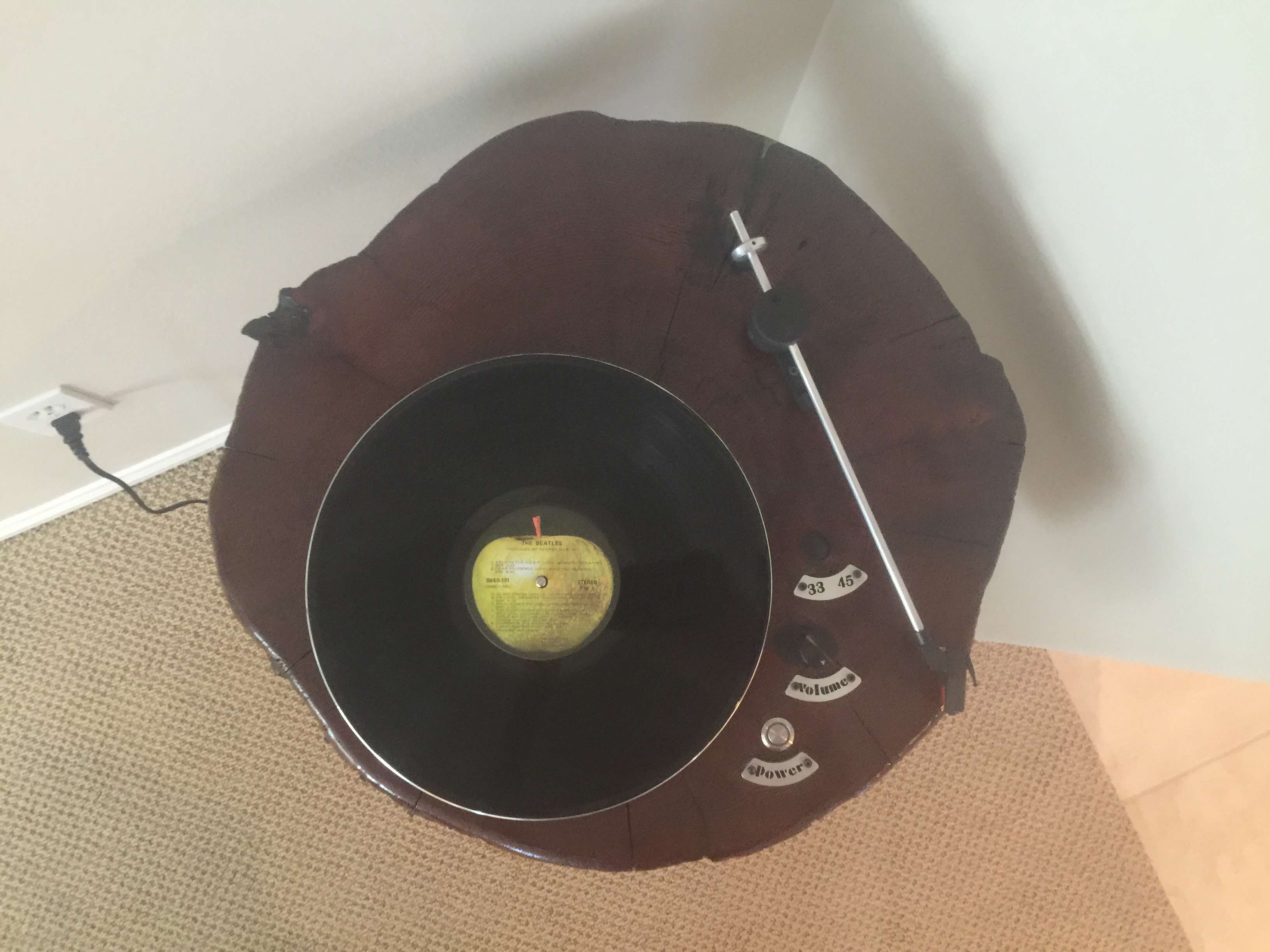